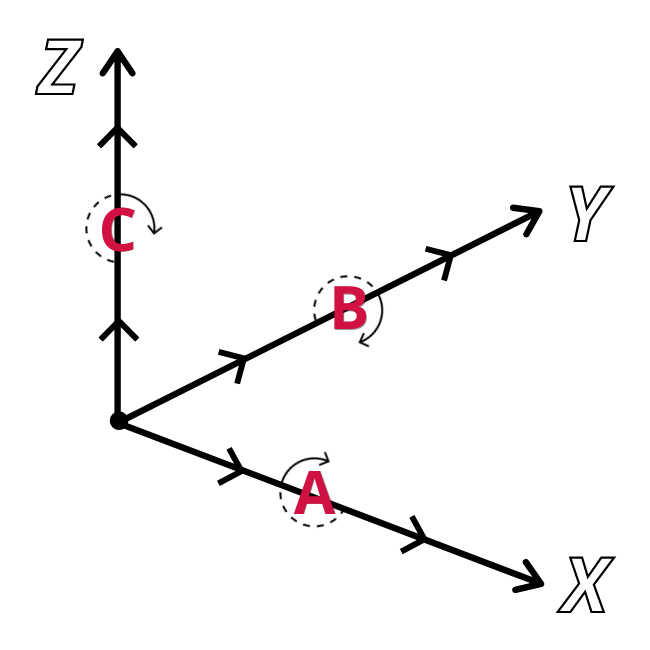
Five-axis machining is taking the machining world by storm, and for good reason. This type of manufacturing, in which computer numerical control is used to move cutting parts or tools along five different axes simultaneously, unlocks incredible potential for any shop. Five Axis Machines reduces labor hours, eliminates extra setups, increases production efficiency, and results in beautiful, complex parts. Understanding 5-axis machining is less simple, though. To help, we are breaking down each of the five axes below.
What are the three basic axes?
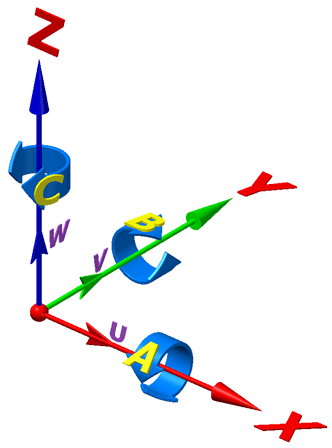
Standard 3-axis milling takes place on the X-, Y-, and Z-axes. These three linear axes are the directions the spindle or part—depending on the machine—can move:
- X-axis: Left-to-right
- Y-axis: Forward-to-back
- Z-axis: Up-and-down
Using all three axes at once, a machine can shave down material to create various three-dimensional objects. It is most useful in situations where the part does not require advanced work-holding, does not have deep or narrow cavities, and can be machined with one setup. For more complex parts, 5-axis machining is better.